
Mobile Home Setup “The Footsteps Guide”
Mobile Home Setup – “A Professional Guide”
Mobile home setup is less challenging if you follow these simple footsteps. Additionally, be mindful that safety is key which includes doing the job right. Moreover, whether purchasing your home from a dealership, factory direct or moving the home to a new location the home comes with an installation manual. However, the manual may not be available for used homes so you will need to use your states mobile home setup prescriptive guidebook.
Installation Manuals
Keeping in mind understanding installation manuals or prescriptive method guidebooks takes regular training. Therefore, your state requires classes for mobile home installers with initial training and periodic course updates. Not to mention, dealerships generally provide professional installations accomplished professionals when purchasing their homes. Nevertheless, I advise finding a professional mobile home setup contractor whenever possible.
Footstep One – Permits
Applying for permits for moving and or setting up a new or used mobile home is required. So, finding your local county, city or burrow’s building department or land use office is mandatory. If you’re doing this within a mobile home park you need to consult the park manager.
Footstep Two – Site Preparation
Preparing your property for your new home is termed “site prep.” Site prep consists of leveling the ground (groundwork), installing cable TV, phone, electrical, gas, water and sewer lines. In the case your site does not already have these services it will be necessary for you to have a licensed professional add them.
Footstep Three – Foundation
Establishing the base for a mobile home setup is key. Moreover, after establishing grade in good bearing soils it’s time for constructing the foundation. Although there are many manufactured home foundation options to choose from, I will only mention one here.
Still, I feel the best option is using a compacted crushed gravel pad of at least 4” thickness with a proprietary earthquake / wind tie-down system (step seven). Additionally, because of the speed and durability of this option, after the compacting the gravel you’re ready to bring the home on site. Furthermore, this manufactured home foundation option is accepted in most if not all jurisdictions.
Footstep Four – Mobile Home Step- Spotting the Mobile Home
Next is spotting the mobile home on your gravel pad. Now the fun begins and depending upon your homes’ new site you may or may not need a crawler. In other words, a crawler helps bring each piece of a mobile home into place from the closet location a tractor/truck can get.
Furthermore, sometimes it may be miles away navigating hills, bushes, trees and other obstacles. If navigating over dips or gullies you will need a good supply of cribbing. Finally, care needs to be taken so that the home and workers are safe.
Footstep Five – Jacking, Blocking, Tie-downs & Connecting
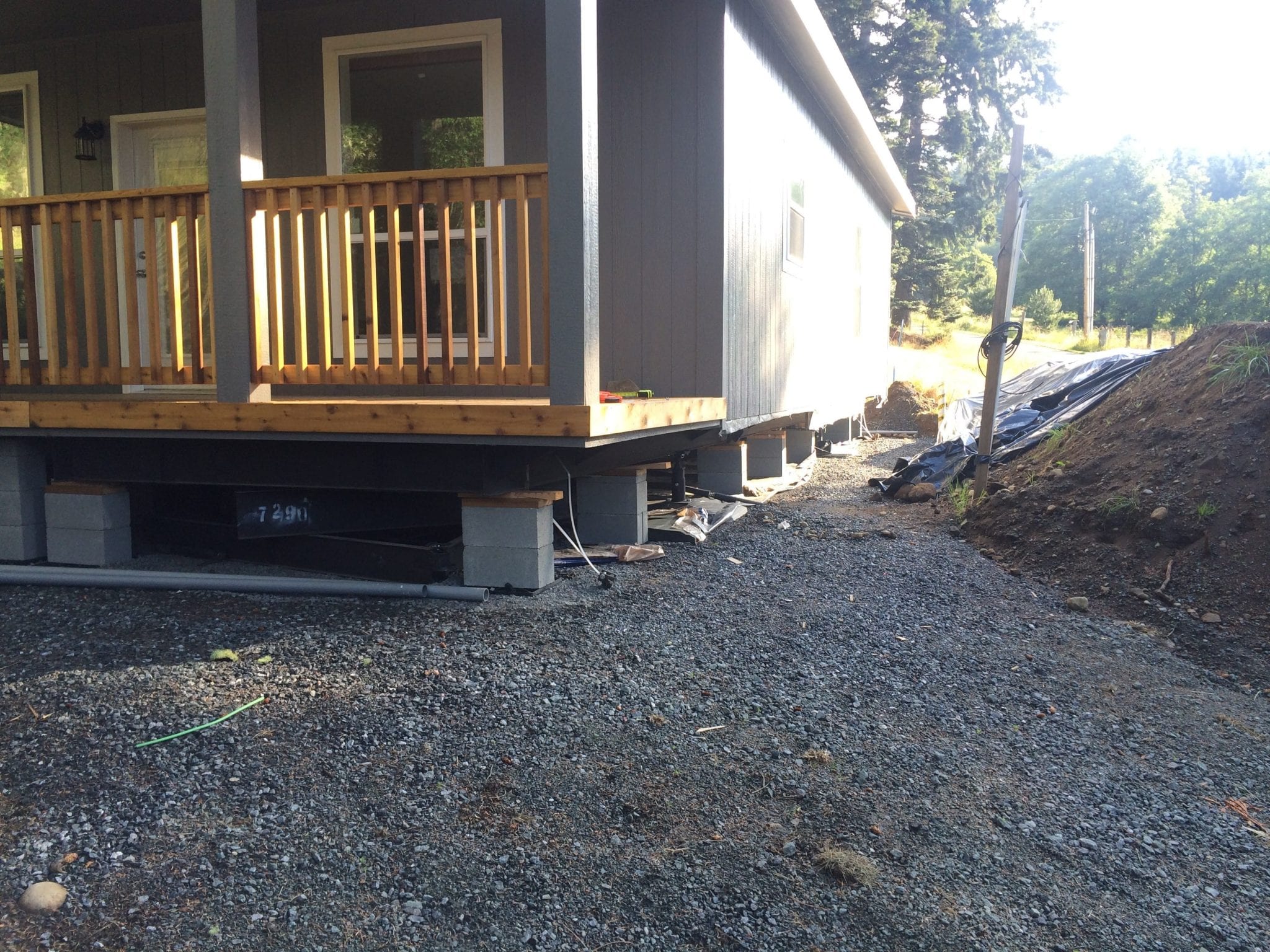
A mobile home setup using the prescriptive guide book.
Now that the home is in place you can begin the blocking and tie-down process. This process consists of installing blocks, shims and wedges at intervals following the manufacturers manual according to the proper snow load. I do not recommend steel jack stands because they can rust away.
Also, I need to point out that the blocking is different for perimeters, beams and marriage lines. Too, are calculated load points on the marriage lines where open spaces occur and requiring more support. Not to mention, while blocking the home you need to remove the tires and axles (step six).
Important for mobile home setup is connecting the home (double, triples & pods) to the ground. Indeed, this is done by following the instruction manual using hardware sent by the factory. Particularly the roof, walls and floors need lagged together so they become one functioning unit.
Using cribbing, jacks and rolling hardware bring the home up steadily to the elevation you need. Also, consider the sewer drainage making sure you have adequate fall. Likewise, making sure home does not encroach into the minimum properties’ setbacks.
Now begin lowering the home onto the block stands you previously laid out in the correct sequences according to the manufactures’ specifications. Moreover, considering the snow load as these effects the blocking concentration.
Footstep Six – Removing Tires, Axles and Hitch(es)
Removing tires, axles and hitch(es) is accomplished while blocking the home. The tires and axles are recycled while the hitch(es) are removed and set back under the home. It is not a good idea to permanently remove the hitches form the home unless of course the home is setting on a basement.
Footstep Seven – Earthquake Resistant Bracing Systems
In most modern home setups this is a required step by lending institutions. As a matter of fact, there are several types of Earthquake Resistant Bracing Systems on the market today. However, many of these systems do not meet HUD Permanent Foundation Code Guidelines and cannot be used for permanent setups. So, be careful which one you choose.
Footstep Eight – Attaching Utilities
There are six common utilities. They are sewer/septic, gas or propane, electricity, water, cable, and phone. Normally water, gas, sewer/septic will need permits and fees paid before installing them. What’s more, is they will need to be inspected for safety. All work and inspections must be done before proceeding to step nine.
Footstep Nine – Interior Floor Alignment
Quality control during a mobile home setup is vitally important. To this end, checking the interior floor of the home to ensure the floor is level. In all areas where the floor is not level, use the jack to ease the load on the foundation pier. Accomplish this by placing wedges or shims between pier and undercarriage of the mobile home to correct the issue. What’s more is keeping an eye on the floor alignment during the process of blocking can save time.
Footstep Ten – Skirting / Underpinning
The final stage of the manufactured homes’ setup is adding skirting or underpinning. Additionally, knowing ahead of time which skirting you’re using is helpful so you can plan the blocking accordingly. If you’re using DURASKIRT™ you should block the home at 31” from rim-joist to ground or concrete pad.
Now that you have read how the setup procedure works on a manufactured home you probably want to hire a professional setup crew like YOUR NAME HERE.
Related Articles
How To Skirt A Manufactured Home Over 38″
Recent Comments